What is Porosity in Welding: Crucial Tips for Getting Flawless Welds
What is Porosity in Welding: Crucial Tips for Getting Flawless Welds
Blog Article
Porosity in Welding: Identifying Common Issues and Implementing Ideal Practices for Prevention
Porosity in welding is a pervasive concern that usually goes undetected up until it causes significant troubles with the stability of welds. This common issue can jeopardize the toughness and toughness of bonded structures, positioning security risks and resulting in costly rework. By recognizing the origin of porosity and carrying out efficient avoidance strategies, welders can substantially enhance the high quality and dependability of their welds. In this discussion, we will discover the vital factors adding to porosity development, analyze its harmful impacts on weld performance, and talk about the very best practices that can be taken on to reduce porosity incident in welding processes.
Common Reasons For Porosity
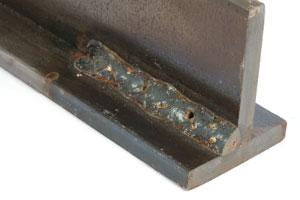
Utilizing dirty or wet filler materials can present impurities into the weld, adding to porosity concerns. To mitigate these common causes of porosity, comprehensive cleaning of base metals, proper securing gas selection, and adherence to ideal welding criteria are important practices in achieving top notch, porosity-free welds.
Impact of Porosity on Weld High Quality

The visibility of porosity in welding can dramatically jeopardize the structural honesty and mechanical homes of welded joints. Porosity creates voids within the weld metal, weakening its total strength and load-bearing ability.
Welds with high porosity levels have a tendency to exhibit reduced effect toughness and minimized capability to deform plastically before fracturing. Porosity can restrain the weld's capability to effectively transmit forces, leading to premature weld failure and possible security threats in vital frameworks.
Finest Practices for Porosity Avoidance
To improve the architectural integrity and top quality of welded joints, what specific actions can be carried out to reduce the occurrence of porosity during the welding procedure? Porosity avoidance in welding is important to ensure the honesty and toughness of the last weld. One reliable look here technique is appropriate cleaning of the base steel, eliminating any impurities such as corrosion, oil, paint, or dampness that can cause gas entrapment. Guaranteeing that the welding devices remains in good condition, with clean consumables and appropriate gas flow prices, can likewise dramatically lower porosity. In addition, keeping a steady arc and controlling the welding parameters, such as voltage, present, and travel rate, assists produce a regular weld pool that lessens the risk of gas entrapment. Using the appropriate welding method for the details material being welded, such as adjusting the welding angle and gun setting, can reference better protect against porosity. Regular evaluation of welds and instant remediation of any kind of problems identified throughout the welding process are essential practices to stop porosity and produce top notch welds.
Value of Correct Welding Strategies
Carrying out correct welding methods is vital in making sure the architectural stability and high quality of welded joints, building on the foundation of reliable porosity avoidance procedures. Welding methods directly impact the overall toughness and longevity of the bonded framework. One crucial facet of proper welding techniques is preserving the proper warmth input. Excessive heat can lead to raised porosity as a result of the entrapment of gases in the weld pool. Conversely, insufficient warmth may lead to incomplete combination, creating prospective powerlessness in the joint. In addition, using the ideal welding criteria, such as voltage, existing, and travel rate, is important for achieving audio welds with minimal porosity.
Moreover, the choice of welding procedure, whether it be MIG, TIG, or stick welding, should align with the specific needs of the job to make sure optimal outcomes. Correct cleaning and prep work of the you could look here base metal, along with selecting the ideal filler product, are likewise vital components of proficient welding techniques. By adhering to these finest methods, welders can lessen the threat of porosity development and create top quality, structurally audio welds.

Testing and Quality Assurance Steps
Checking procedures are vital to discover and avoid porosity in welding, guaranteeing the strength and resilience of the last item. Non-destructive testing approaches such as ultrasonic testing, radiographic testing, and visual examination are frequently utilized to recognize possible flaws like porosity.
Carrying out pre-weld and post-weld evaluations is also essential in maintaining top quality control standards. Pre-weld assessments entail confirming the products, devices settings, and cleanliness of the workplace to avoid contamination. Post-weld evaluations, on the various other hand, evaluate the last weld for any type of flaws, including porosity, and verify that it fulfills defined standards. Executing a thorough quality assurance plan that consists of comprehensive testing procedures and examinations is critical to reducing porosity issues and guaranteeing the total high quality of bonded joints.
Final Thought
In final thought, porosity in welding can be an usual concern that influences the quality of welds. By identifying the common reasons of porosity and carrying out ideal practices for prevention, such as proper welding methods and screening procedures, welders can make certain high quality and dependable welds. It is important to focus on avoidance methods to lessen the occurrence of porosity and keep the integrity of welded structures.
Report this page